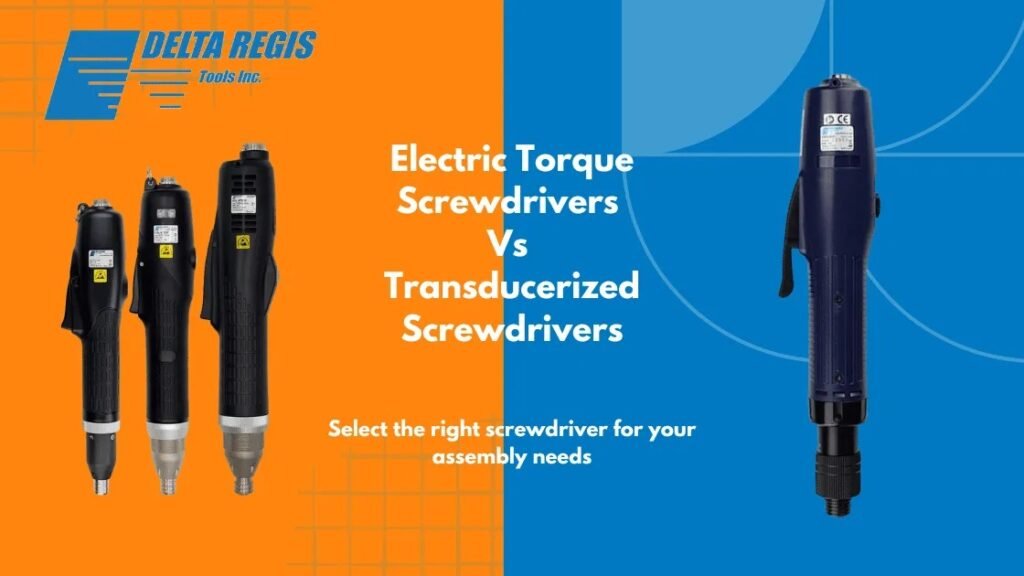
Smooth-running assembly lines rely on properly preloaded fasteners. But inconsistent tightening can sabotage production pace. Manual wrenching leaves too much room for human error while basic power tools lack smart torque control. This is why advanced electric screwdrivers are rapidly becoming the go-to for efficiently driving screws, bolts and other threaded fasteners to specified target torque.
Yet many plant managers or purchasing agents feel apprehensive about switching from longtime manual tools to powered alternatives. Cost, complexity and reliability misconceptions fuel resistance to evaluating their comparative value. Below we bust myths around electric torque screwdrivers versus manual wrenches to give clear guidance on what best optimizes assembly line torque efficiency.
The Problem With Manual Torque Wrenches
Torque wrenches seem simple enough. Just set the dial to the needed torque value, fit it to the fastener head, and twist until it “releases” signaling target tightness is achieved. But hidden downsides plague manual operation:
Inconsistent Technique – Humans don’t apply perfectly steady force when pulling on wrenches. This leads some fasteners over or under tightened despite using torque wrenches.
- Fatigue Factor – Manually hitting high torque values hundreds of times daily fatigues workers. As muscles tire, torque technique suffers further.
- No Data Tracking – Manual wrenches don’t record tightening data for quality audits. Undetected drifts from target specs are risks.
- Slow Speed – Each individual fastener must be laboriously tightened via hand power alone. This throttles workflow pace.
- Frequent Calibration Need – The calibration of all manual torque wrenches tends to drift from repetitive dropping or overloading misuse.
- Added Cost – Employing more workers to meet production schedules due to slow manual wrenching gets expensive fast.
These realities highlight how traditional non-powered wrenches bottleneck modern lean teams striving for Six Sigma quality levels today. Thankfully electrification provides solutions.
Electric Torque Screwdrivers Deliver Speed, Accuracy and Data Tracing
Power tool innovation enables precision electric torque screwdrivers programmed to shut off upon reaching preset target torque values. This prevents over tightening while their advanced features solve other manual wrenching weaknesses:
- Programmable Control – With electronic torque menus and memory settings aligned to each fastener, guesswork and variability goes away.
- Rapid Drive Speeds – Power tools drive fasteners significantly faster over wrench waving arms so each worker handles more.
- Loosening Ability – Electric models don’t just tighten accurately but also loosen stuck bolts better if needed.
- Comfort Factor – Pulling triggers ergonomically beats manual torque force, reducing fatiguing strain.
- Smart Data Logging – Every electric fastening data point gets captured to SD card tracing torque histories to the individual bolt level.
- Long Calibration Stability – Advanced electric torque accuracy holds steady between annual certified recalibrations
Overall electric torque screwdrivers enhance each aspect of precision, speed and traceability across production rotors. And new fastening inspection abilities now emerging take environments leveraging these to fuller modernization.
Integrated Vision Inspection – The latest electric torque drivers integrate downward facing cameras visually confirming proper flushness, fill and other details about the actual joint fastened for the ultimate quality lock.
The Range of Electric Torque Screwdriver Choices
With clearer advantages over manual wrenches, plant managers next face selecting the optimal electric tool specifications for their workflow. Diverse styles and brands serving niche fastening needs can complicate choices. Use this guide to hone decisions:
Torque Ranges – Electric screwdrivers offer target torques spanning lighter electronics applications below 10 Nm up to driving truck wheel lug nuts over 3000 Nm. Choose appropriate tool capacity for each fastening.
Rotational Speed – The fastest electric drivers spin small screws in under one second while slower high torque variants take 10-15 seconds for bigger bolts. Faster models align to high volume small technology assembly.
- Single/Multi-Speed – Variable speed electric torque screwdrivers allow starting slower before accelerating to full RPM preventing thread stripping or camming out. Fixed single speed types suit heavy joint seating.
- Manual Override Ability – Some electric torque screwdrivers allow manual power off then finishing tightening a few turns by hand to account for minute gasket compression variables.
- Angle Control Models – Top-end electric torque screwdrivers sense angle rotation which confirms final snugging completeness even if the torque value was already met.
- Smart Network Integration – For advanced Industry 4.0 smart factories, networked electric torque screwdrivers embed wireless communication for central analytics.
By itemizing needed capabilities per application then matching to the feature sets and calibration ranges offered by precision electric torque screwdriver suppliers, managers obtain maximum line efficiencies.
Why Choose Flexible Assembly Systems?
This brings us to where to obtain your energy-accelerating electric torque tools for sustaining screwdriving productivity. Having demonstrated the clear advantages of electric torque screwdrivers over primitive manual wrenches, plant managers must select an equipment vendor possessing application expertise plus the product range meeting all tightening needs. Flexible Assembly Systems stands out as the premier one-stop supplier best supporting operations from initial consultation through tool selection, acquisition, training, implementation and lifetime product service/support.
Flexible Assembly Systems earns your electric torque screwdriver business by delivering you total value beyond just selling tools including:
Free Custom Torque Spec Guidance – With over 30 years advising diverse assembly industries on optimizing torque techniques, Flexible Assembly Systems’ experts help managers appropriately spec target parameters.
Widest Electric Torque Screwdriver Selection – We offer the deepest range spanning low torque electronic assembly to high strength structural fastening across all tool ergonomics.
Budget Conscious Packages – Avoid overspending on fancier tools with more features than application needs. Our tailored bundles match lower prices to functionality required.
Operator Training – Ensure smooth electric tool adoption through Flexible Assembly Systems customized on-site instruction ensuring proficient operation for torque confidence.
Annual Calibrations – We provide free test & recalibration services restoring your electric torque screwdrivers to factory accuracy.
Real-Time Data Monitoring – Cloud connect tools to our Telemetry portal for complete enterprise-wide torque analytics.
Unconditional Lifetime Service – All our electric torque screwdrivers carry no-questions-asked lifetime service guarantees for worry-free usage.
To upgrade assembly line fastening, put Flexible Assembly Systems’ torque expertise and 30 year reputation for empowering manufacturing innovators to work for you. Contact our electric torque screwdriver specialists today for a complementary line evaluation identifying opportunities. The efficiencies uncovered will quickly justify upgrading manual operations to the smarter precision of electronic torque tooling.